Exploring the Advantages of Plastic Injection Tooling Made in China
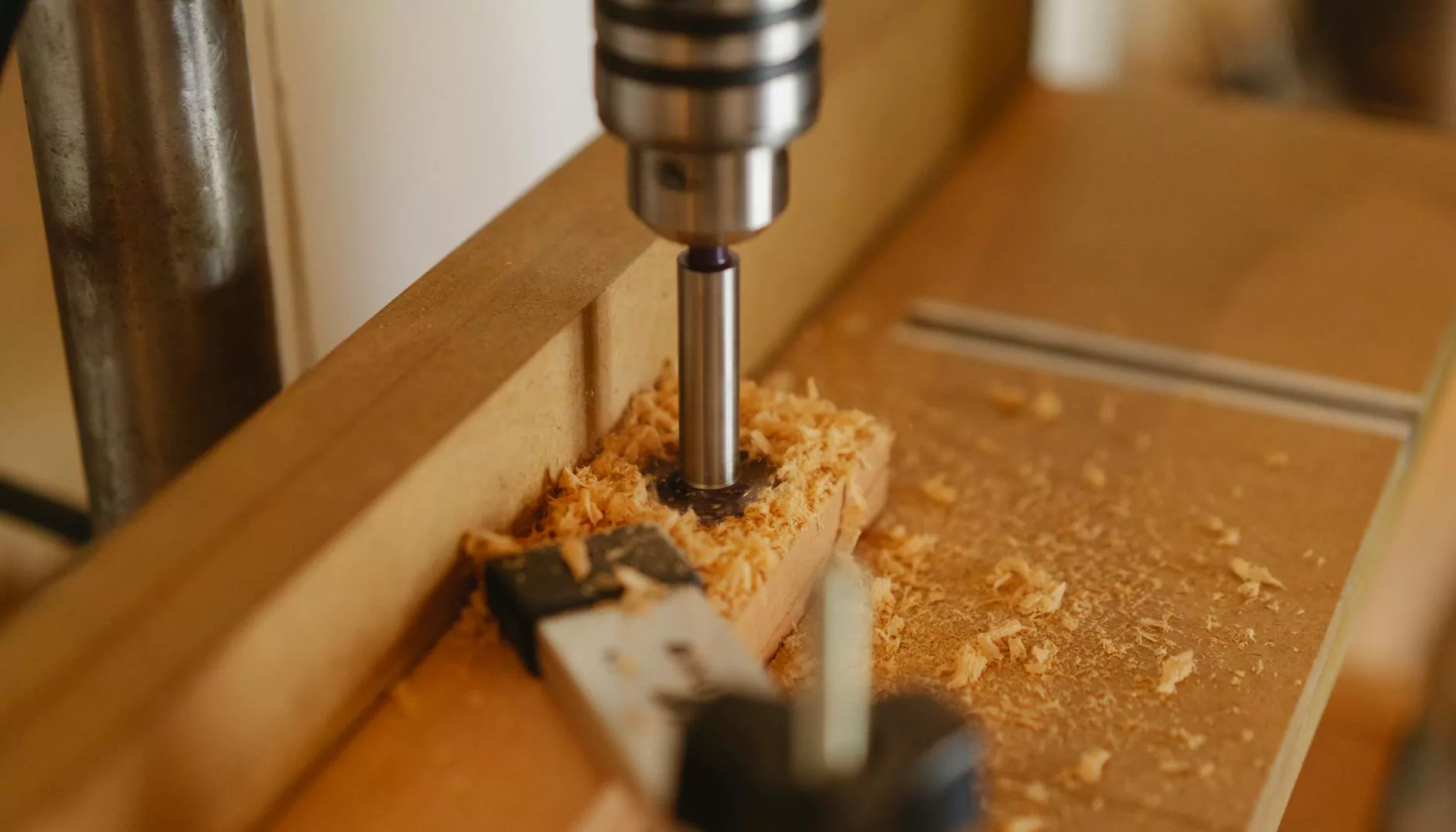
Plastic injection tooling made in China has revolutionized the manufacturing landscape, enabling businesses to produce high-quality products at lower costs. This article delves into the intricacies of plastic injection tooling, its benefits, and its pivotal role in the manufacturing industry, especially for metal fabricators.
The Mechanics of Plastic Injection Molding
Plastic injection molding is a manufacturing process that involves injecting molten plastic into a mold. This process is highly efficient for producing complex parts in large quantities. The key stages of plastic injection molding include:
- Mold Design: The initial phase involves designing the mold, which is crucial for ensuring precision and quality in the final product.
- Material Selection: Various types of plastics can be used depending on the required properties of the finished product.
- Injection: The molten plastic is injected into the mold under high pressure, ensuring that it fills every cavity.
- Cooling: The part cools and solidifies within the mold, taking the shape of the desired product.
- Ejection: Once cooled, the part is ejected from the mold for finishing and packaging.
The Importance of Quality in Tooling
When it comes to plastic injection tooling made in China, quality is paramount. Chinese manufacturers have made significant advancements in technology and machinery that allow for the production of high-precision molds. Factors that contribute to the quality of tooling include:
- Material Quality: High-grade steel and alloys are used to manufacture molds, ensuring durability and longevity.
- Precision Machining: Advanced CNC (Computer Numerical Control) machines provide the precision required for complex designs.
- Expert Craftsmanship: Skilled artisans in China are adept at mold-making, ensuring that every detail is executed to perfection.
Advantages of Sourcing Plastic Injection Tooling from China
Choosing to source plastic injection tooling made in China presents several advantages for businesses looking to optimize their manufacturing process:
Cost Efficiency
China has established itself as a hub for manufacturing due to lower labor costs and economies of scale. Businesses benefit from:
- Reduced manufacturing costs, allowing for competitive pricing.
- Access to a wide range of suppliers and manufacturers, facilitating price negotiations.
- Ability to allocate savings towards other areas, such as innovation and marketing.
Access to Advanced Technology
Chinese manufacturers boast sophisticated technologies and methodologies in plastic injection molding:
- Utilizing the latest machinery, enhancing production efficiency and product quality.
- Integration of automation and robotics to improve consistency and reduce human error.
- Adoption of best practices and innovations from global leaders in the industry.
Scalability and Flexibility
Manufacturers in China offer scalability that is often unrivaled:
- Ability to increase production volume quickly to meet demand surges.
- Flexibility to adjust designs and specifications according to client feedback and market trends.
Case Studies: Successful Implementation of Chinese Tooling
The success stories of companies utilizing plastic injection tooling made in China are abundant. Here are two notable examples:
Case Study 1: Automotive Industry
A leading automotive company faced challenges with component production costs. By partnering with a Chinese tooling manufacturer, they achieved:
- A 30% reduction in tooling costs.
- Improved lead times by 40%, thanks to rapid prototyping capabilities.
- Higher customer satisfaction with improved component quality and consistency.
Case Study 2: Consumer Electronics
A consumer electronics brand sought innovative designs for new products. Their collaboration with a Chinese manufacturer resulted in:
- The development of intricate designs not feasible with their previous suppliers.
- Significant cost savings that allowed them to invest in marketing and product features.
- A robust supply chain capable of handling international shipping and compliance with regulations.
Challenges and Considerations
While there are substantial benefits to sourcing plastic injection tooling made in China, businesses should also consider potential challenges:
- Communication Barriers: Language differences may lead to misunderstandings. It’s advisable to work with bilingual representatives.
- Quality Control: Implementing stringent quality control processes is essential to ensure that the final products meet industry standards.
- Intellectual Property Protection: Ensure appropriate measures are taken to protect sensitive designs and patents when dealing with overseas manufacturers.
Strategies for Successful Partnership with Chinese Tooling Manufacturers
To maximize the benefits of plastic injection tooling made in China, businesses should adopt strategic approaches:
Thorough Research
Invest time into researching and identifying reputable manufacturers. Look for:
- Established track records and customer reviews.
- Certifications and adherence to international standards.
- Specializations that align with specific production needs.
Building Relationships
Developing a strong relationship with manufacturers can lead to better service and flexibility. Consider:
- Regular communication to ensure alignment on project goals.
- Visits to manufacturing facilities to foster trust and transparency.
- Long-term partnerships that encourage collaboration on future projects.
Implementing Quality Control Processes
To avoid production issues, businesses should implement robust quality control measures, including:
- Regular inspections and audits at the manufacturing site.
- Verification of raw materials and tooling processes.
- Collaboration on setting benchmarks and performance indicators.
The Future of Plastic Injection Tooling in China
The future of plastic injection tooling made in China looks promising. As technology continues to advance:
- The integration of smart manufacturing and Industry 4.0 practices will enhance efficiency.
- Investment in R&D will drive innovation in tooling design and materials.
- A focus on sustainability will lead to greener practices in production processes.
Conclusion
In conclusion, plastic injection tooling made in China is not just a manufacturing option; it is a gateway to quality, efficiency, and innovation in production. By leveraging the advantages and addressing challenges through strategic partnerships, businesses can unlock new potentials in their operations. As the demand for high-quality components continues to grow, so does the importance of understanding and utilizing the capabilities offered by Chinese tooling manufacturers.
To explore how your business can benefit from these advancements in manufacturing, visit us at deepmould.net.